Technical Design
Much has happened on our self-build eco-home at Belfry Alley since our last blog post. After receiving planning consent we produced a technical design for the house, have completed the groundworks and are halfway through building the timber structure!

This blog focuses on the technical design stage that enabled us to pass building control and produce our own cost estimate for the build. In this stage Amy and I made many decisions about the foundations, structure, and thermal envelope of the house. In summary, the key decisions were:
The foundation will be a reinforced slab - this has the benefit of minimising the amount of excavation, and avoiding the need for a party wall agreement with the flats to the north because the formation level (depth to bottom of foundations) is much shallower than traditional trench fill. Moreover, this type of foundation could alleviate concerns relating to past coal mining risk because any subsidence caused by potential cavities lurking underground could be overcome by the rigidity of reinforced slab. This meant we did not need to undertake a very costly intrusive survey for coal mining (bore hole core sampling). Most importantly however, we required a foundation type that could cope with any volume change in the soil due to the location of our soakaway that had to be much closer to the building then regulations usually allow. George Holland from Element Structures skilfully demonstrated to Building Control that the low plasticity index of the soil, along with a high degree of reinforcement would ensure the foundations could cope with high amounts of water movement.
The structure will be timber - timber is low carbon and a familiar form of construction for me and my builder friends. Access to the site is restricted so the timber structure cannot be prefabricated; instead, a stick build method is employed. We chose solid timber (as opposed to timber I beams) to save costs. To reduce waste, we realised that all structural parts could be in the same timber: the walls, the floor, and the roofs are all in 195mm x 45mm treated softwood. Using timber also meant that lower U-values (higher thermal resistance) could be achieved with a thinner wall thickness. We decided on glulam beams over steel for the large sway frame and ridge beams. Exposed glulam gives a warm, natural feel and the embodied carbon of wood is far less than steel. The glulam beam over the living area weighs over 220kg which would need thinking about for safe construction.

The envelope shall breathe – using natural materials for the building envelope will enable the structure to breath (accept and release water vapour). The system we chose is almost identical to the build-up we employed at Fawley Eco-house (explained in this blog-post), with propassive OSB internal racking, blown cellulose infill insulation, and wood-fibre boards for both roof and walls. Here though, we opted for a lime render external finish for the walls; to be applied directly over the wood-fibre insulation. Of key importance therefore, is that the render is hydroscopic; allowing water vapour to pass which is crucial to ensure the timber structure inside does not rot. Hydraulic lime render is very breathable and is much more forgiving than traditional cement or silicon-based renders and can be patched up easily.

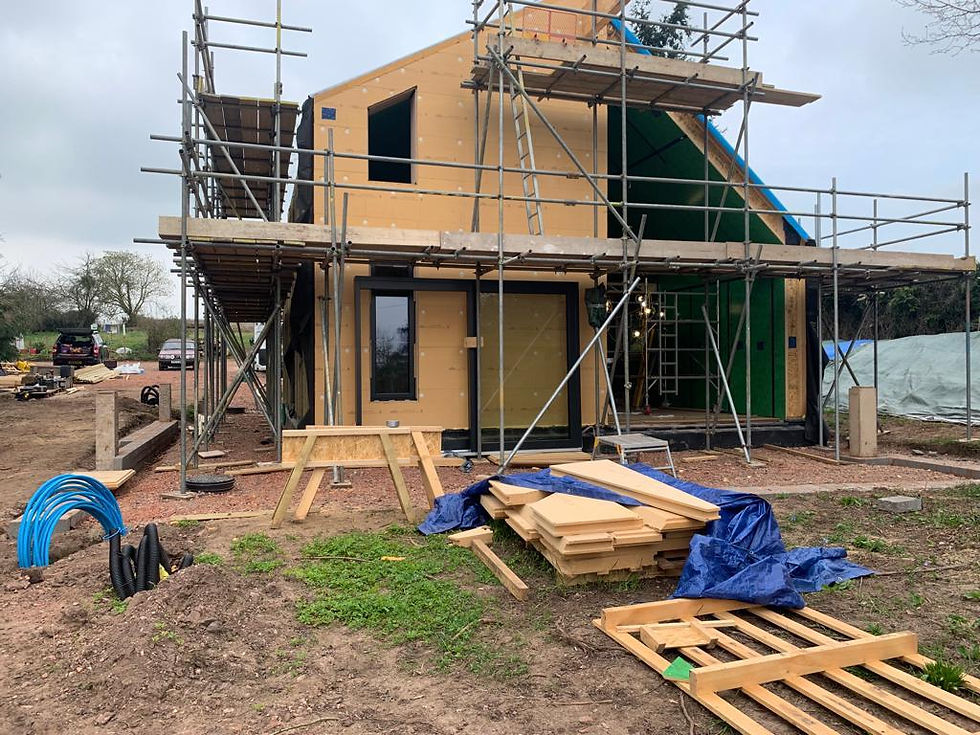
We will aim for the AECB Building Standard for energy efficiency – We want a warm home with tiny heating bills (especially now that energy prices are off the charts), but don’t have the money to create a passive house. One step down, the AECB Building Standard is a low-risk option that will "reduce overall CO2 emissions by 70% compared to the UK average for homes – a highly significant result given the relative ease and low cost with which this standard can be met." Achieving the target will mean:
Low-U values - for wall (0.14w/m2K), roof (0.13w/m2K), and floor (0.15w/m2k)
Thermal bridge free detailing - paying attention to the junctions to ensure there are no cold spots.
Super airtightness - a (n50) of <1.5h-1 is required which takes care and attention at both design and construction stage to achieve.
Less than 10% summer overheating - this is becoming more of an issue these days so we have horizontal louvres over some areas of glazing.
Mechanical Ventilation with Heat Recovery (MVHR) - this will ensure a healthy supply of fresh air (for us and the fabric of the building) whilst capturing the heat from expelled, stale air.
Expensive windows - with low U-values and good air-tightness (*subject to budget constraints!!)
Modelling the house in using the Passive House Planning Package (PHPP). I can use this software and can self-certify the AECB Building Standard.

We will calculate embodied carbon - We wish to meet the RIBA 2030 Challenge for embodied carbon, and will use the PHribbon plugin to calculate the embodied carbon of the shell of the house from 'Cradle to Grave', covering stages A-C of the RICS methodology. I am pretty certain that the wall and roof construction can achieve the target of < 625 kgCO2e/m2, but the huge amount of steel and concrete in the ground floor slab will be the deciding factor.
Budgeting
But what if we can’t afford all that? In truth, we can’t...we’ve calculated it. We know that we will run out of money; we are just hoping we run out once the roof is on and the place is secure and watertight. We can then slowly work on the inside of the house (including second fix electrics and plumbing) when funds become available. We will have cold running water, a temporary electrical supply, and a fully insulated envelope to keep us alive…it’ll be fine.
We spent a great deal of time creating a cost estimate for the build. We did this by breaking down each stage of construction, starting from the ground up, and listing all the materials and labour we would require. Not having done this before, we knew that there would be plenty of ‘unknown unknowns’ so we added 10% on to our calculations to account for our naivety and wishful thinking.
Our estimate puts us at just over £100,000 to reach watertight shell, equating to a cost per m2 of £1,064. This excludes professional fees such as engineering but does include servicing the plot with water and electricity. It assumes that we do a lot of the work ourselves to reduce costs. We expect there will be another circa £50,000 to spend after watertight shell for the internal fit out, although this will depend very much on our taste for finishes and fittings, and how inventive we can be! The table below gives the cost targets for each milestone of the build. The groundworks are expensive because of the amount of reinforcement. The MVHR and ASHP are big outlays for the M&E, and so is the lime rendering and windows for the envelope.

Key to saving costs is managing the project ourselves. A typical build would be managed by a main contractor who would deservedly charge a percentage (usually around 15-25%) for overheads and profits. Managing the build ourselves means we avoid these costs but it does add significant stress, risk, and time to the project. More fun though too.
Banks & Warranties
Briefly, as it may be of interest to some, let’s discuss warranties and mortgages!
We have opted for an unusual form of construction. Warranty providers and lenders don’t like anything unusual. This seems to be a problem in the industry because the choice of construction system is ultimately decided by whatever your structural warranty provider or bank is willing to accept. Do these people have training in construction? Are they architects or builders? How can we progress new forms of construction if those giving the green light don’t know a thing about green construction?
I have heard of prospective buyers of new-build homes constructed in timber being unable to purchase because their bank will not put up a mortgage for a timber building! Come on, we have been building in timber for centuries, and if correctly detailed will last just as long as concrete block, not to mention help save our planet.

Luckily, we avoided this conversation with our bank by not borrowing any money for the build. Doing so would have placed too many restrictions on it, and we would have had to pay for the bank's surveyor to assess the works. We did however agree that a structural warranty was a good idea, so went about finding a provider. The majority were happy with timber construction and actually had little concern of our breathable system for the envelope. We opted for Self Build Zone in the end as they came in lowest on price and seemed most flexible with 'Modern Methods of Construction'. They checked the technical drawings prior to construction and gave us preliminary approval without any major amendments to the design. They visit at key milestones (groundworks, structure, envelope, etc) to sign off the work.
Next blog
We will be back soon with a commentary of the first, and most unnerving stage of construction; Groundworks….
Comments